There are many different project management methodologies: Agile, Waterfall, V-shaped, Scrum... Discover how the Kanban method can transform your organization by optimizing tasks and processes for a more efficient team.
1. What is the Kanban Project Management Method: definition, origins and application
2. Fundamental principles of the Kanban method
3. Key practices and tips for optimal use of Kanban
4. How to implement the Kanban system in your company
5. Kanban or Scrum method: which one to choose?
6. Challenges and limits of Kanban implementation
What is the Kanban Project Management Method: definition, origins and application
Definition
Kanban is a visual project management method that enables you to track tasks in real time, manage priorities and promote team collaboration. The Kanban method is based on a philosophy of continuous improvement, where tasks are methodically extracted from a set of requests (backlog) to create a fluid, harmonious workflow. It aims to manage workflow by visualizing these tasks using signal cards. The word 'Kanban' translates literally as 'sign' or 'map' in Japanese.
-
-
Kanban's origins in production flow
To fully understand the origins of the Kanban method, we need to go back to the 1940s at Toyota factories in Japan. Inspired by American supermarkets, where shelves were replenished as sales progressed, engineer Taiichi Ohno developed an approach in which "Kanban cards" represented production and inventory requirements. This pull-flow structure, which depended on market demand rather than anticipated overproduction, optimized resource management and improved team efficiency. Adopted for its Lean approach to reducing waste, the Kanban method laid the foundations for lean manufacturing. Toyota was able to balance customer demand with production more effectively, making Kanban an adaptable and continuous management model.
Application of the Kanban methodology
Today, the Kanban method has established itself as an indispensable framework. Nevertheless, different applications of this project management metrhodology exist.
- Production Kanban applies particularly to industrial environments, to optimize the management of material and part flows in manufacturing processes. This system uses labels or cards to signal the need for production or replenishment of specific items, facilitating a continuous flow without stock-outs. In this approach, a workstation triggers production when needed, enabling better resource management and reduced lead times, while limiting intermediate stocks for greater efficiency.
- The Handling or Transport Kanban is used to manage the movement of inventory within the supply chain. This type of kanban is essential for signalling a need for product replenishment, either to feed a downstream station in a production process, or to transfer items from a warehouse to a point of sale, such as a store shelf. This method optimizes movements, ensures continuous product availability, and reduces replenishment lead times, contributing to smoother, more responsive inventory management.
- Kanban Digital, ore-Kanban, is a computerized version of the Kanban method, enabling automated management of information flows and requests in a production or project environment. This approach, which is the most frequently encountered today, particularly in software development, relies on digital tools to transmit the needs of each work stage in real time. e-Kanban enhances the flexibility and responsiveness of processes, making it particularly suitable for evolving environments and teams requiring effective visual management.
Would you like FocusTribes to help you find the best talent to support your projects?
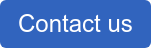
The fundamental principles of the Kanban method
Start with Existing Processes
The Kanban method recommends starting with practices already in place. Unlike other management methods that require radical changes, Kanban allows teams to integrate existing workflows. This approach reduces disruption and ensures a smooth transition to more efficient task management. By identifying processes that are working well, Kanban encourages gradual evolution without upsetting the whole organization.
Promoting Progressive and Evolving Change
A fundamental principle of Kanban is to introduce changes gradually. Rather than sudden reforms, the emphasis is on continuous improvement, avoiding the resistance often associated with major changes. This approach encourages teams to adjust processes bit by bit, based on feedback and optimization of practices.
Encouraging leadership at all levels
Kanban values shared leadership, where every team member is encouraged to actively contribute to improvements. This principle promotes accountability and stimulates innovation. By giving everyone a voice, the whole team can participate in the evolution of working methods, creating a collaborative and motivating environment for achieving optimum performance.
Focus on Service Delivery
Finally, the Kanban method places customer satisfaction at the heart of its priorities. Teams focus on the quality and speed of services in response to customer needs and expectations. By managing workflows and optimizing services, Kanban helps guarantee a high level of service, enabling value to be delivered while avoiding micromanagement.
Key practices andtips for optimal use of Kanban
-
-
- Columns, representing the different stages of the workflow, provide a clear, structured overview, enabling teams to visualize progress in real time.
-
- Cards, meanwhile, embody individual tasks, providing authentic transparency and facilitating prioritization.
-
- Each step taken by a card through the columns symbolizes progress towards completion, encouraging fluid collaboration and continuous improvement.
-
By adopting this approach, teams can not only optimize their productivity, but also strengthen trust and commitment within the collective.
-
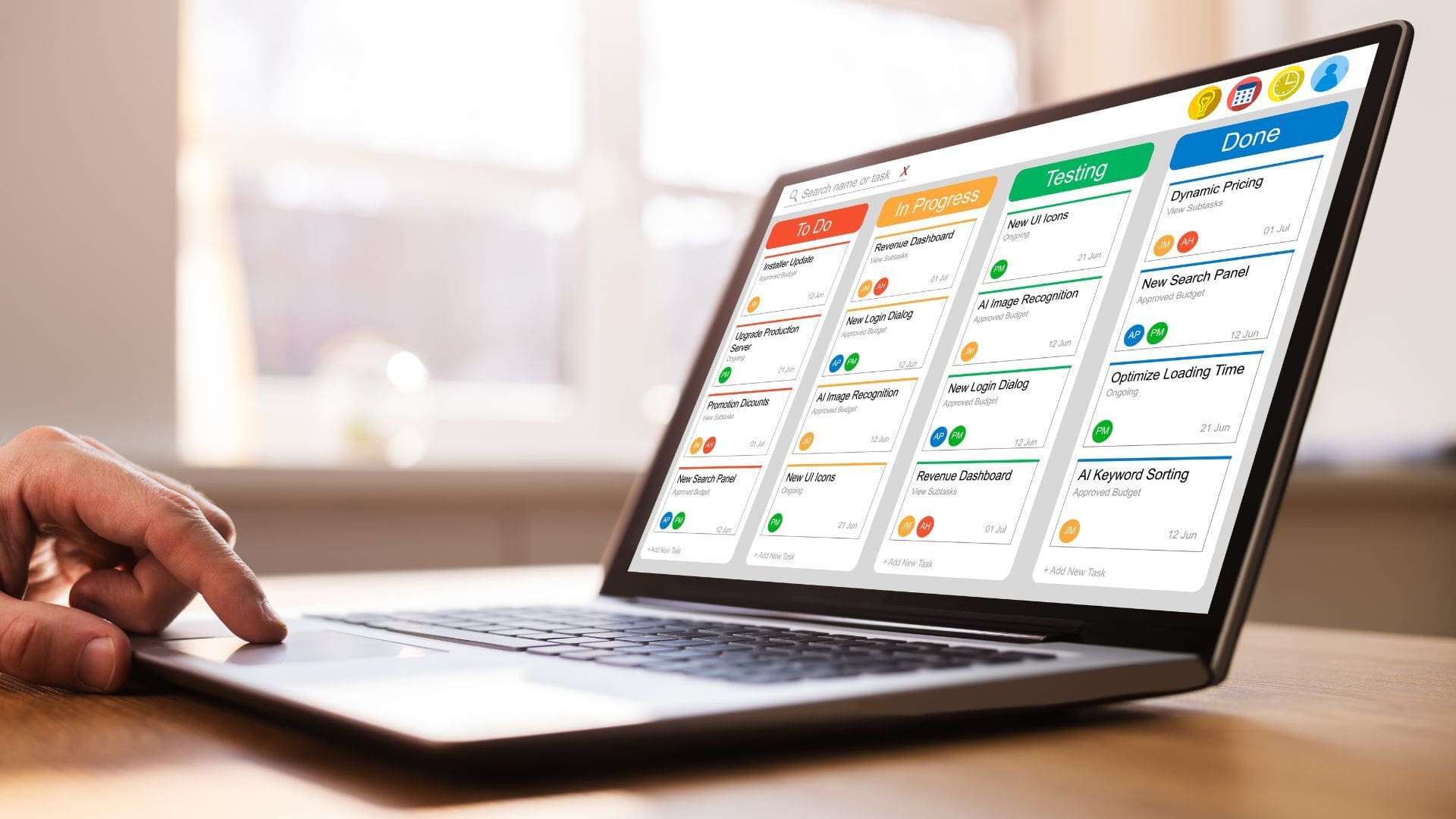
-
-
-
Limit Work In Progress (WIP) to optimize productivity
-
An essential principle of the Kanban method is Work In Progress (WIP). By restricting the number of tasks a team can manage simultaneously, we encourage greater concentration and avoid dispersal of effort. This innovative approach helps to reduce delivery times, by encouraging teams to focus on a restricted set of tasks until they are completed, thus guaranteeing optimum efficiency and superior quality.
-
Managing workflow to improve team efficiency
In the Kanban method, workflow is constantly optimized to ensure smooth, seamless progress.Flow metrics such as lead time and cycle time play a crucial role in improving work efficiency. By integrating these tools with systems such as Scrum, companies can structure their services to meet deadlines and optimize collective performance. Continuous improvement, or Kaizen, plays a crucial role in Kanban: regular adjustments enable the process to be adapted to the specific needs of the team and to constantly changing working conditions.
Clearly defining the Kanban operating process
To optimize the effectiveness of the Kanban method, it is essential to define and share clear operating standards with the team. These standards, which provide a framework for the workflow, enable everyone to understand the essential steps and criteria for task progress. Involving employees in drawing up these rules fosters collective commitment and greater adherence to Kanban practices. In addition, transparent and scalable work policies encourage self-organization and initiative, guaranteeing a lasting positive impact on productivity.
-
Fostering a feedback culture
To establish a true feedback culture within the Kanban method, it's essential to set up regular feedback loops at all levels. This starts with daily meetings, such as the Kanban meeting, where each team member shares his or her progress and goals for the day.
In addition, it's crucial to gather feedback from both the team and customers. Customer feedback helps to assess the relevance and effectiveness of the products or services delivered, while internal feedback helps to identify areas for process improvement. Both types of feedback offer a valuable opportunity to adjust the team's standards and practices, ensuring that they evolve continuously and are adapted to the dynamic working environment.
How can you implement the Kanban system in your company?
Mapping flows for better prioritization
To effectively integrate the Kanban system into your company, start with a thorough analysis of current work processes. It's crucial to map these flows to identify inefficiencies and establish clear priorities. Once you've done this, introduce the Kanban board as an innovative visual tool for tracking tasks in real time. This board should reflect the essential stages of each project, from planning to delivery, ensuring fluid, agile process management.
Train employees in the Kanban method
Training employees in the Kanban method is a crucial step in guaranteeing its success. Each team member must grasp the fundamental principles of Kanban, such as workflow, work-in-progress (WIP) limits, and feedback cadences. Training must be interactive, with hands-on workshops and simulations, to facilitate rapid adaptation to this innovative system. By reinforcing the culture of feedback and communication, teams will be able to fully exploit the benefits of the Kanban method.
Customize the Kanban board to your company's processes
The Kanban board needs to be adapted to reflect the specifics of your company's processes. Depending on team size and project complexity, adjust the columns, cards and colors to better represent the workflow. The aim is to make the chart as clear and intuitive as possible, enabling each team member to track tasks in real time. Integrating digital tools, such as Kanban project management software, can also improve the visibility and accessibility of information, while enabling dynamic task management and continuous process evolution.
Kanban or Scrum method: which one to choose?
-
-
Advantages of the Kanban Method for large companies
The Kanban Method offers many advantages for large companies. It provides a clear view of the workflow, making it easier to identify inefficiencies and bottlenecks. By limiting work in progress, Kanban helps to reduce stress and improve the quality of work.
What's more, Kanban fosters a culture of continuous improvement by encouraging teams to regularly review and optimize their processes. This can lead to a significant increase in productivity and employee satisfaction. Finally, the increased transparency and flexibility offered by Kanban enable better management of priorities and resources.
-
-
Differences and similarities between Kanban and Scrum
-
Kanban and Scrum are two agile methodologies used for project management, but they differ in their approach. Kanban is flexible, based on a continuous workflow with no defined sprints, and focuses on managing the flow of tasks according to priorities. In contrast, Scrum works in iterations or sprints, with defined roles (Scrum Master, Product Owner) and regular ceremonies, such as retrospectives and sprint reviews. In terms of similarities, both approaches aim to improve efficiency, encourage team collaboration, and promote visual task management, often via Kanban boards. Companies can choose either method according to their specific needs, or even combine elements of both to optimize their project management.
-
-
Assessing objectives, the nature of tasks, and team dynamics is crucial to making an informed choice between these two agile methods.
Challenges and limits of Kanban implementation
Although Kanban offers many advantages, its implementation can also present certain challenges.
Resistance to change
One of the main obstacles is resistance to change on the part of employees, who may be reluctant to adopt new ways of working. It's crucial to communicate the benefits of Kanban transparently, and to involve teams early on in the process, to promote a smooth transition.
The need for rigorous discipline
Another challenge lies in respecting work-in-progress (WIP) limits and keeping the Kanban board up to date. Kanban may not be suitable for all types of project. For example, for a team managing a large number of tasks, the situation can quickly become complex. Before implementing this project management method on a large scale, you can test the implementation of one process at a time.
So it's important to recognize that Kanban may not be suitable for every type of project. If its fundamental principles are in line with the way your teams operate, this project management method will seem self-evident. If doubts remain, it may be wise to combine Kanban with other project management methodologies, such as Scrum, to adapt to the specific requirements of your projects and take advantage of Kanban's benefits. In short, careful assessment of project needs and strategic adaptation of the Kanban method are essential to overcome these challenges and maximize its effectiveness.
Do you want the Focustribes team by your side and access to the best talent to support your projects?
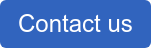